Energy efficient tobacco curing barn launched at Kutsaga
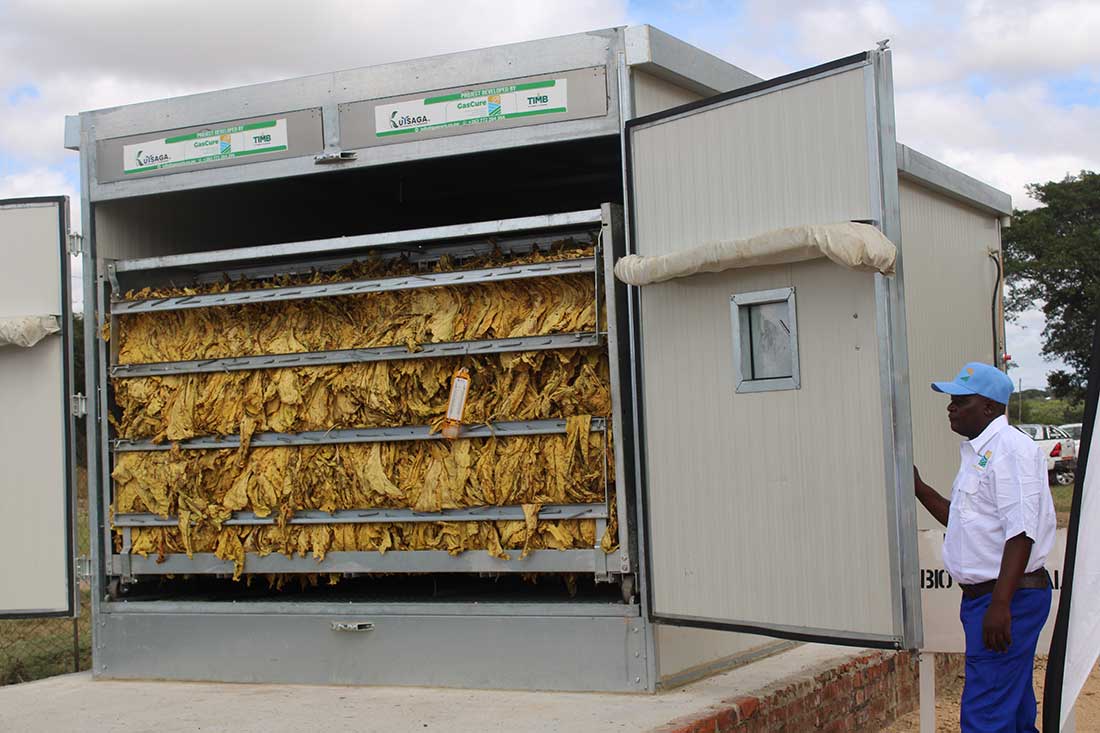
Research into a cleaner, sustainable alternative tobacco curing fuel for Zimbabwe’s gold leaf is showing promising results with the commissioning of a gas curing barn.
Kutsaga Research Station, in partnership with the Tobacco Industry and Marketing Board (TIMB) and private players Gas Cure, officially commissioned the gas curing barn in late March.
The trials are the result of a transformative partnership for the long-term benefit of our tobacco sector. As TIMB board chairman, Patrick Devenish commented in the speech read on his behalf by TIMB board member Mrs Makuku, “collaboration is key to our drive of enhancing industry sustainability and improving livelihoods of our hard-working farmers. As an industry we need to cement such private/public partnerships.”
Speaking at the occasion earlier, Kutsaga Board chairman, Aaron Denenga, reminded guests of the pressing need for sustainable practices in tobacco production. “The World Health Organisation Framework Convention on Tobacco Control (WHO FCTC) has underscored the urgency of adopting environmentally friendly methods. Our commitment to the cause has led us to explore alternative solutions, and the LPG/Biogas barn stands as a testament to our dedication.”
“LPG offers a cleaner, more efficient way to cure tobacco leaf. By harnessing the power of LPG, we reduce our carbon footprint, minimise deforestation and ensure a healthier environment for generations to come.“
This comes at a time when, the world over, tobacco production is coming under fire from multiple fronts on the sustainability front. In Zimbabwe, tobacco remains the top-earning cash crop and is grown by over 134,000 registered growers (source: TIMB). Not only does it support the livelihoods of these growers, their families and their communities, but the tobacco value chain is at the heart of our agro-based economy, feeding into several businesses in the country.
However, as it is a global commodity, adherence to compliance and sustainability must remain at the forefront of production. “There is need to stay informed about industry trends, market demands and regulatory changes. We need to keep an eye on emerging technologies, consumer preferences, and health regulations to ensure the gas curing plant remains at the forefront of the industry,” Mrs Makuku said.
Whilst the data gathering exercise is ongoing, the first season’s curing trials were underway at the occasion and guests were invited to see firsthand, the process and its cured tobacco.
The gas barn has been meticulously designed and rigorously tested to deliver consistent, high quality curing results.
Quick stats
- Requires approximately 40 per cent less investment compared to chongololo and tunnel
- Saves time and labour - reaped tobacco does not need to be tied on strings or in clips
- Even distribution of heat and humidity
- Monitoring can be digitalised, automated management
- One bin carries tobacco equivalent to one trolley
- Improved quality with a uniform cure across the barn
- The barn can work on both biogas and LPG
- The curing cycle at Kutsaga is six days.
- The unit is both scaleable and moveable. A comparison to a coal tunnel system reveals the following:
- Energy efficiency, 0.48 - 0.64 kg of fuel needed to cure a kg of tobacco compared to 1.2 kg of coal.
- Carbon emissions per kg of dried tobacco 0.96 kg compared to 2.69 kg for coal.
- Less labour and no clips are needed meaning reduced inputs and labour costs
- Set up cost USD 6,200/ha compared with tunnel at USD 9,000/ha.
- Thermal efficiency is 96.5 per cent.
The gas curing initiative brings with it a 50 per cent cut in carbon emissions, reduced labour and capital requirements and more importantly, an alternative that will protect the environment for a greener and more sustainable future.
The discovery and development of the Muzarabani gas fields means LPG is a plentiful resource. The unit on trial at Kutsaga can use a mixture of biogas and LPG. The biogas digester is fed on a mixture of vegetable waste and livestock slurry. The circle of sustainability is completed with the solid waste from the biogas translating into a valuable compost.
Kutsaga research trials run over three seasons before recommendations are given, however, the research board is open to interested farmers wishing to partake in the gas curing barn trials.